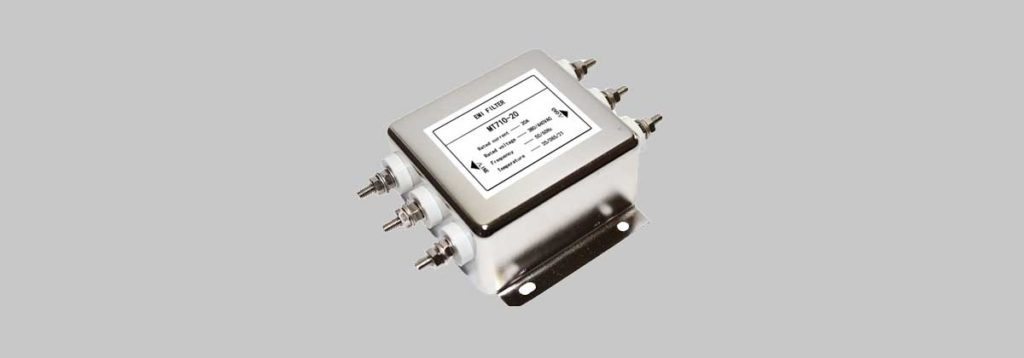
EMI line filters are used in electronic devices, industrial equipment, household appliances and commercial equipment (such as vending machines), to reduce the effects of EMI on the performance of these devices.
Effects of EMI
Electromagnetic emission occurs due to a variation in the flow of electric current. This variation could be caused by natural occurrences such as fire, lightning, or other atmospheric elements.
Artificial sources of electromagnetic emission include all those equipment and devices that are connected to electricity – equipment that runs on power or manages current flow. Industrial power equipment such as capacitors, inductors, transformers, resistors and semiconductors can be artificial sources of conducted EMI.
Interference occurs when the emission enters unintended electrical paths.
Conducted electromagnetic interference is one such form of EMI, which affects by inducing electrical noise. Electrical noise travels to the equipment connected to the power supply line experiencing EMI. This interference affects the equipment’s performance and renders it inadequate for its purported application.
Keeping EMI in check is also important for regulatory purposes. This is because EMI is capable of affecting not just the product connected to the affected supply line but the entire power network connected to the product. Your product must conform to regulatory standards of permissible EMI levels to be considered reliable and legitimate.
Benefits of EMI Line Filters
By reducing the EMI effects, EMI line filters help you comply with EMC (Electromagnetic Compliance) standards, and in keeping the performance of your equipment intact.
EMI line filters find application in two ways. They can be used to control electrical noise generated due to interference within a device, or they can be used to prevent electrical noise generated by other equipment in the vicinity from entering the protected device.
An EMI line filter features a collection of electronic components including capacitors and inductors that achieve the required objective, by forming an L-C circuit. A frequency far higher than that of a normal signal helps an EMI filter identify interference; the inductor part of the filter acts immediately by blocking or displacing the EMI signal.
The capacitor parts of the EMI filter work in tandem with the inductors to block high frequency signals from reaching vulnerable circuits. With all components of an EMI filter working to block any EMI, electrical noise neither enters nor leaves the device using the filter.
Key Parameters to Consider when Buying an EMI Filter
- Operative Frequency – Operative frequency of the EMI filter is an important parameter. EMI filters that work for a wide range of frequencies are always better.
- Operating Current – The type of current (AC or DC) to be used for the application in which the EMI filter is to be used.
- Rated Voltage – This parameter refers to the maximum permissible line voltage that can be used on the EMI line filter.
- Rated Current – This is the maximum permissible current that can be passed to the EMI filter.
- Leakage Current – Measured in milliamperes (mA), leakage current is the amount of current that travels from the filter’s ground terminal when connected to an AC power source. EMI filter with a high leakage current value needs proper grounding or it can cause an electric shock.
- Operating Temperature – The permissible range of ambient temperature at which the EMI filter can be operated.
- Operating Humidity – The permissible range of ambient humidity at which the EMI filter can be operated.
Trust AM Transformers for Quality EMI Line Filters
At AM Transformers, we supply EMI line filters of custom-make as well as regular common mode type. We have been in the transformer industry for more than 20 years, and have been catering to businesses across the UK. We are reputed for our quality products and reliable customer support.